SeaPort-e Quality Assurance
Skyhawk Logistics' Quality Control staff creates project-specific Quality Control Plans for all of our Government contracts to ensure services are performed in accordance with Performance Work Statement (PWS) requirements. We currently have Quality Control Programs at all of our worksites to identify, prevent and ensure non-recurrence of any defective services. This ensures the risk of non-performance is minimized and provides program oversight, control and responsiveness to the Government's requirements.
Skyhawk Logistics' senior management monitors all of our contracts scheduling, work activities and quality control methods used by our personnel while performing the most efficient and successful project operation. Our Project Managers work with company Quality Control Inspectors to ensure that all contract work is performed by our employees in accordance with standard industry methods, safe and the most proficient manner appropriate to the task. We believe that this effective quality control supervision by our Project Manager and corporate quality control personnel, assures good quality assurance and thereby result in the Government's satisfaction and mission success.
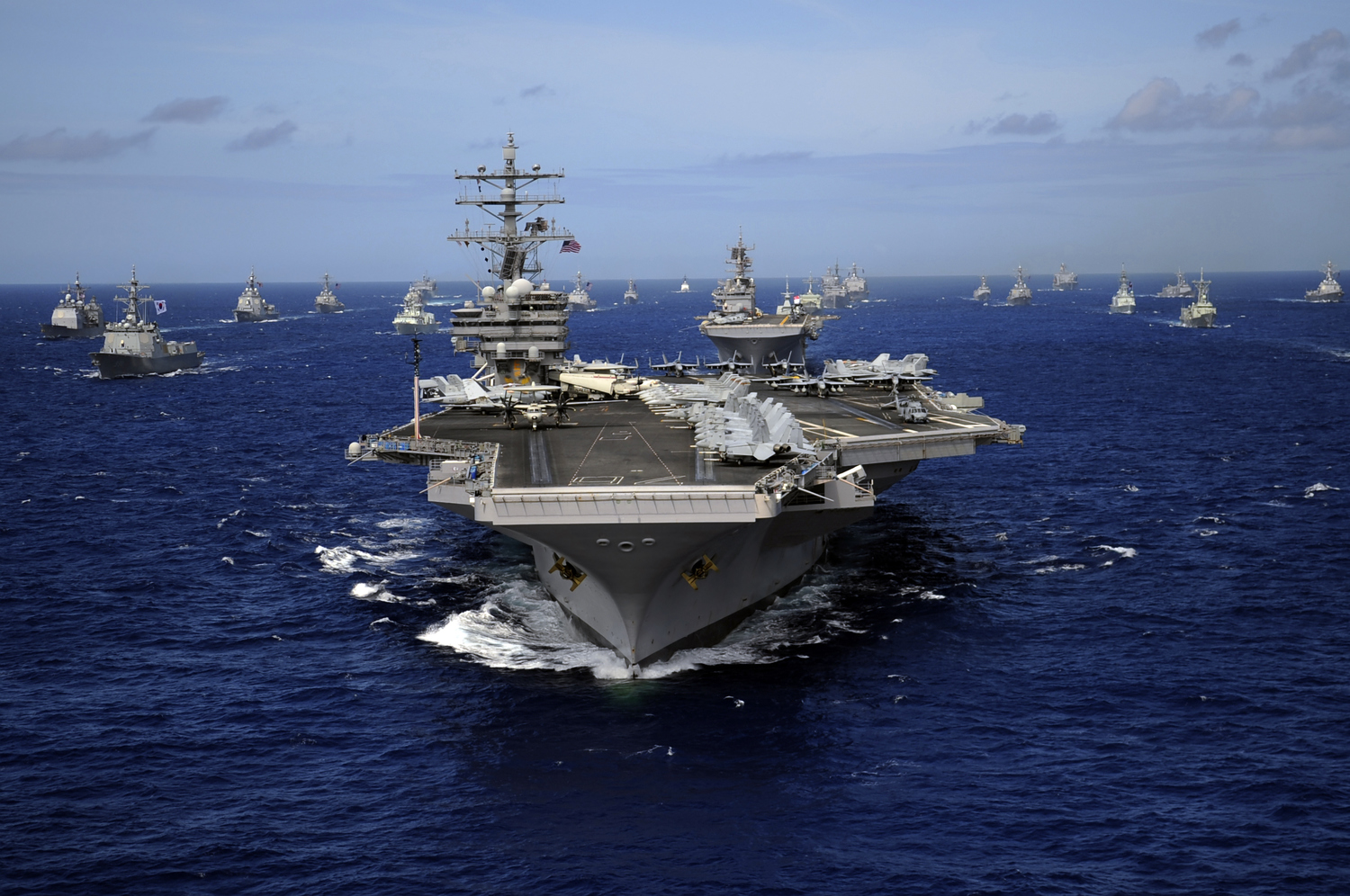
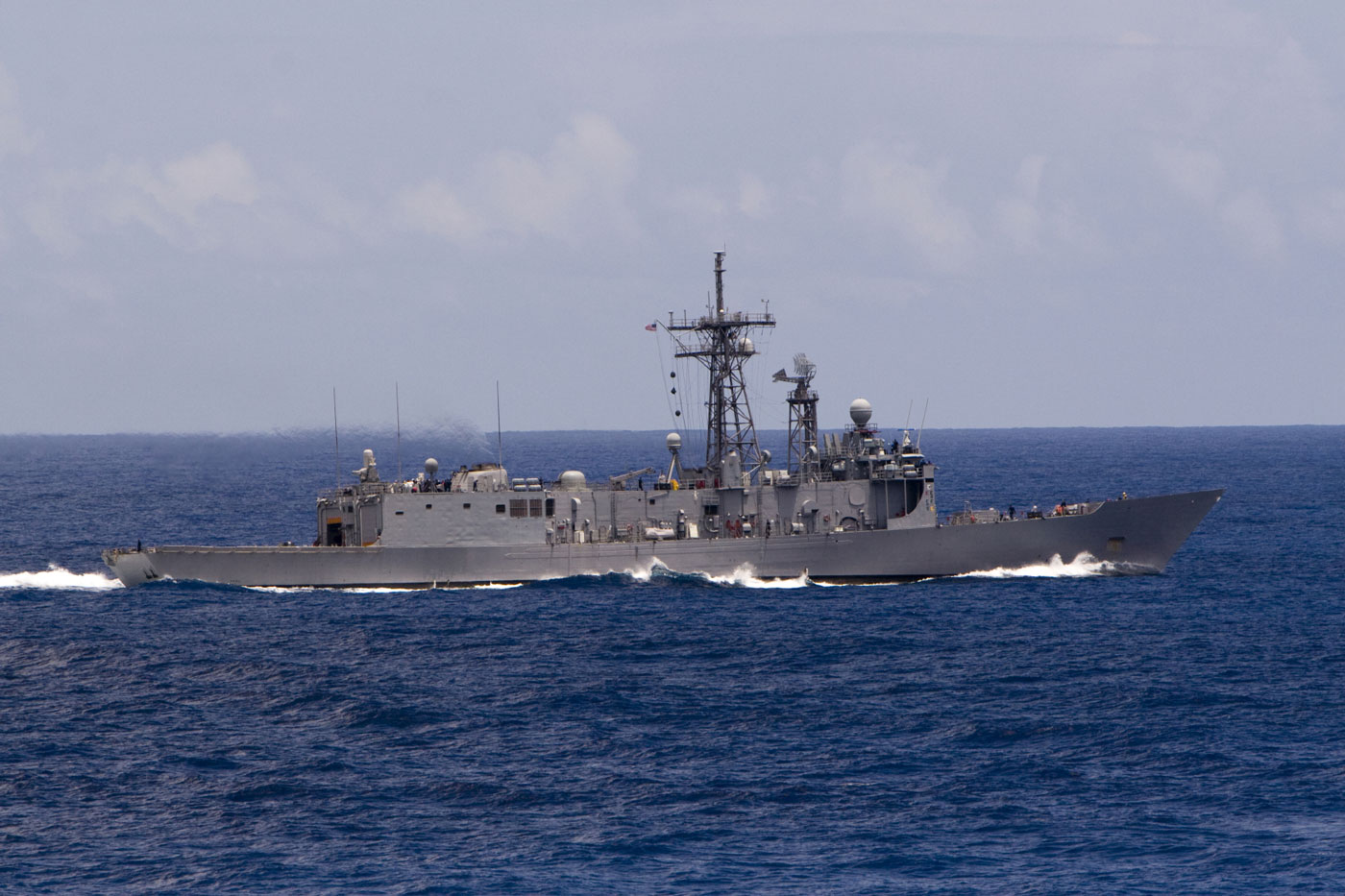
On long term contracts, a member of the corporate quality control staff periodically inspects and observes Skyhawk Logistics' procedures and performance at contract locations. This evaluation process is the basis for on-the-spot corrections to avoid waste and accidents, ensure compliance with contract requirements, as well as assisting in the identification of areas where additional cost-effective procedures might be implemented.
We use Quality Control Checklists to ensure that the inspections encompass each PWS area of contract service. This assists our Project Managers in their day-to-day operations management. Skyhawk Logistics Quality Control Checklists allow for early detection of any issues, conflicts and through our prompt correction actions allow a means of resolution. Our intention is to provide continuous quality improvement, plan for maintaining quality standards in accordance with the PWS. We believe that the end results are a better operation and the best service possible to each of our Government customers.